Utilizing QR Code Management to Shorten Instrument Information Retrieval Time
Original article: https://cli.im/article/detail/1823
We are the Instrument Management QC Team from the Adjustment and Testing Research Institute of State Grid Liaoning Electric Power Research Institute. Our project Utilizing QR Code Management to Shorten Instrument Information Retrieval Time won the 2021 Shenyang Quality Science and Technology Achievement Second Prize. At CaoLiao's invitation, we'd like to share our experience.
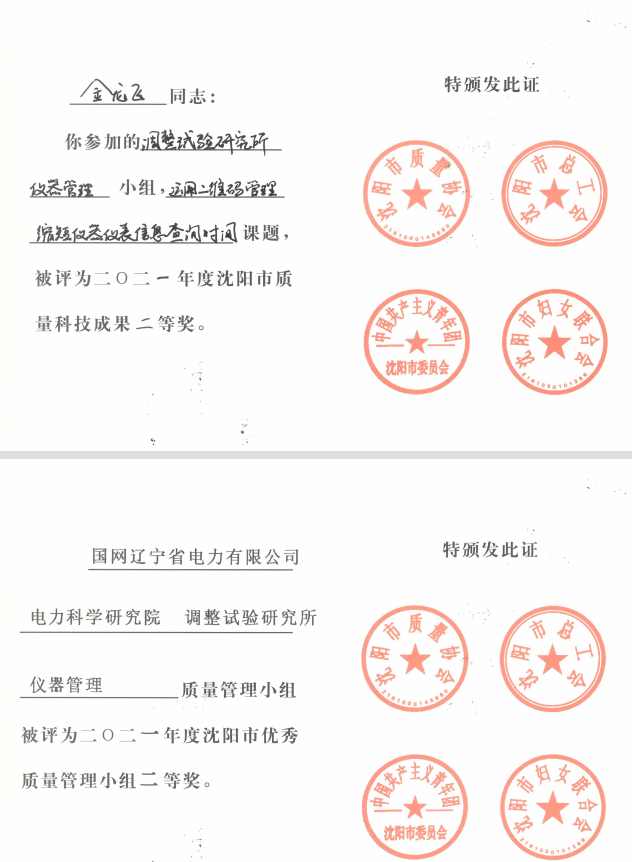
Topic Selection
1. Needs Analysis
Instrument management is crucial for ensuring timely and quality completion of thermal power commissioning projects. With instruments categorized across six major disciplines (turbine, boiler, electrical, thermal control, chemistry, civil engineering), manual tracking of documentation like manuals, calibration reports, and maintenance records caused significant inefficiencies. Our random sampling revealed:
- Minimum retrieval time: 13 minutes
- Maximum retrieval time: 19h50min
- 60% cases required over 5 hours to locate documents
2. Core Requirements
Key challenges identified:
- Difficulty maintaining physical document integrity across projects
- Time-consuming manual check-in/check-out processes
- Lack of real-time maintenance tracking
- Limited accessibility for overseas projects
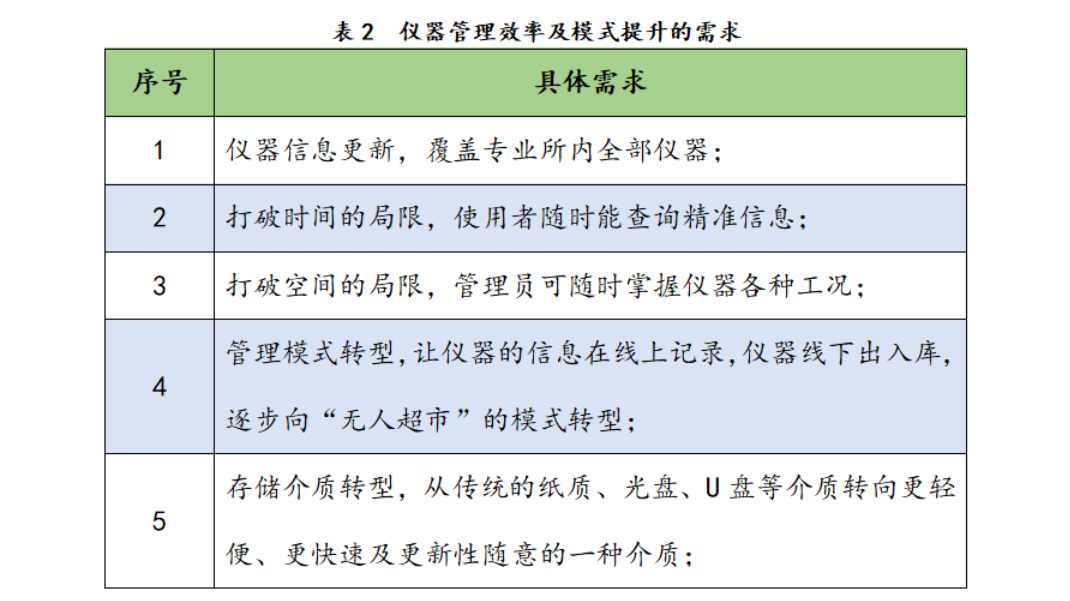
3. Technical Solution
After evaluating existing solutions, we proposed using dynamic QR codes as centralized information carriers with:
- Multi-format document hosting (PDF, video, CAD, etc.)
- Real-time update capabilities
- Permission-based access control
- Automated maintenance request system
Implementation Strategy
1. System Architecture
Three-layer structure:
- Data Layer: Cloud storage for instrument documentation
- Service Layer: Dynamic QR code management platform
- Application Layer: Mobile/web access interfaces

2. Key Features
- Multi-format Support: Tested 15+ file formats including CAD drawings and HD videos
- Hierarchical Access: Role-based permissions for technicians/managers/contractors
- Maintenance Workflow: Integrated check-in/check-out and repair request forms
- Cross-device Compatibility: Optimized display for mobile and desktop
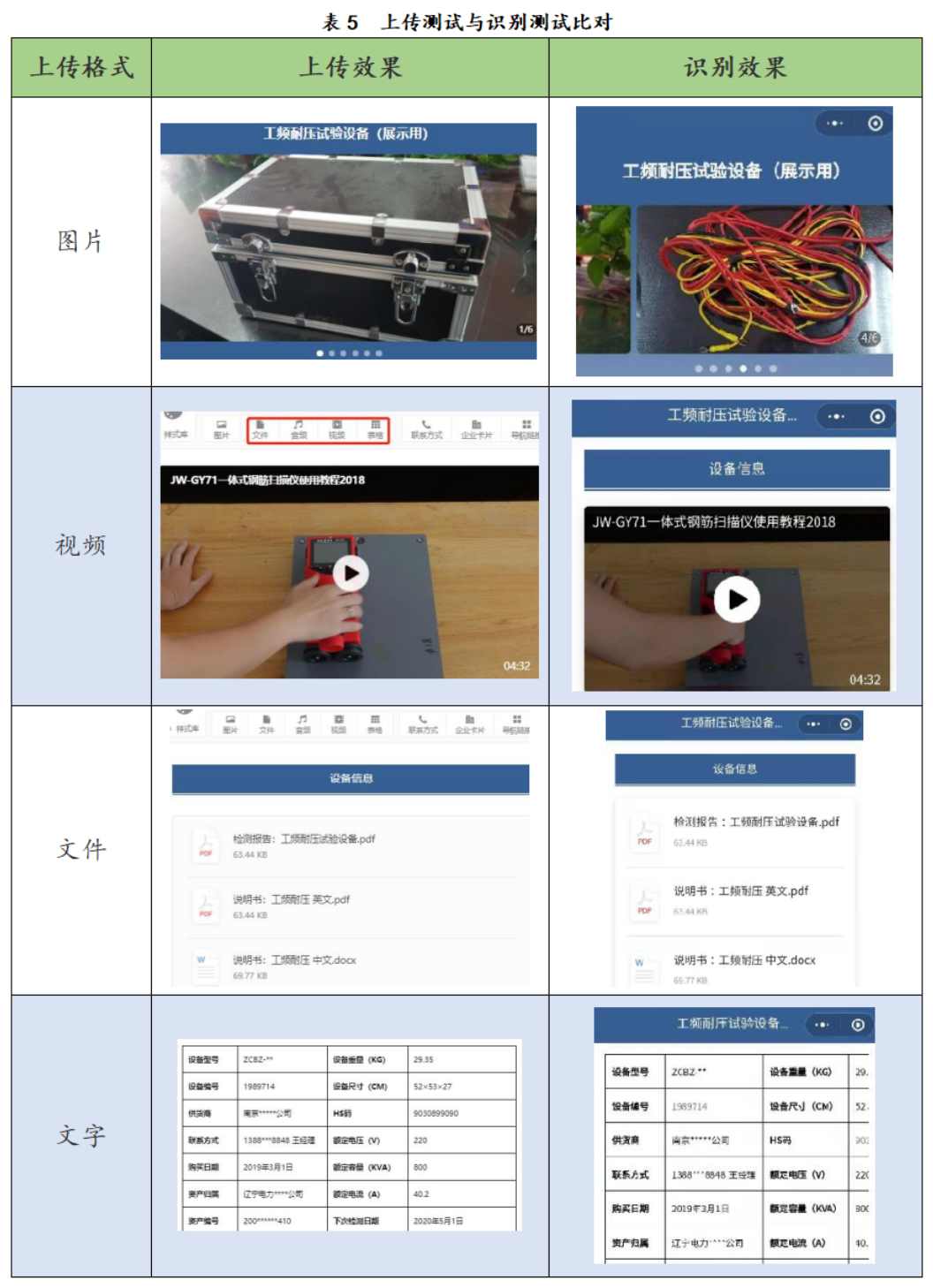
3. Implementation Steps
- Data Standardization
- Unified documentation templates
- Metadata tagging system
- QR Code Deployment
- Laser-engraved stainless steel tags
- Dual-layer encoding (basic info + cloud link)
- Workflow Integration
- Automated inventory tracking
- Real-time maintenance alerts
- Cross-project access management
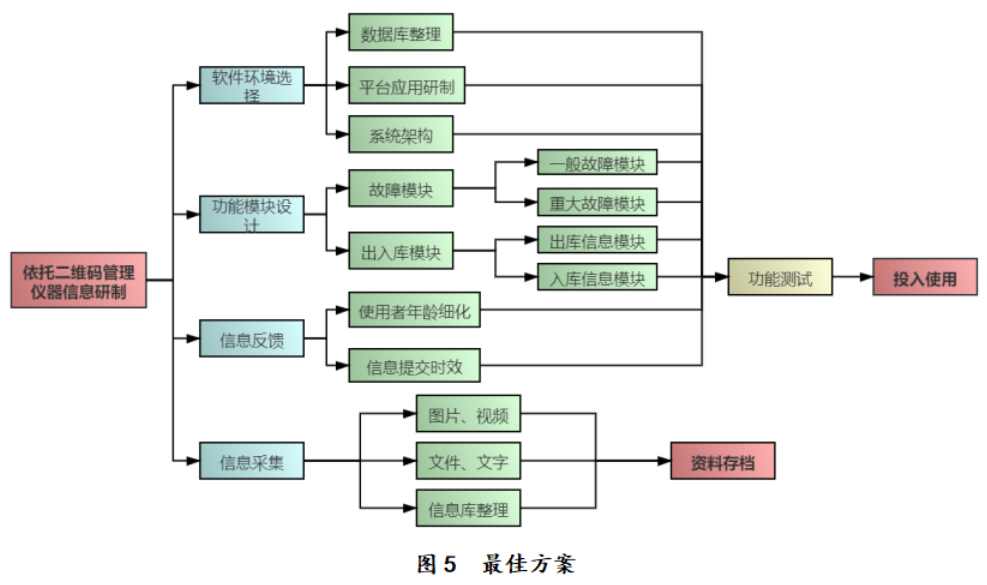
Results
1. Performance Metrics
Indicator | Before Implementation | After Implementation | Improvement |
---|---|---|---|
Avg. Document Retrieval | 5h23min | 8.5s | 99.96% |
Inventory Accuracy | 87% | 99.8% | 12.8% |
Maintenance Response Time | 48h | 2h | 95.8% |
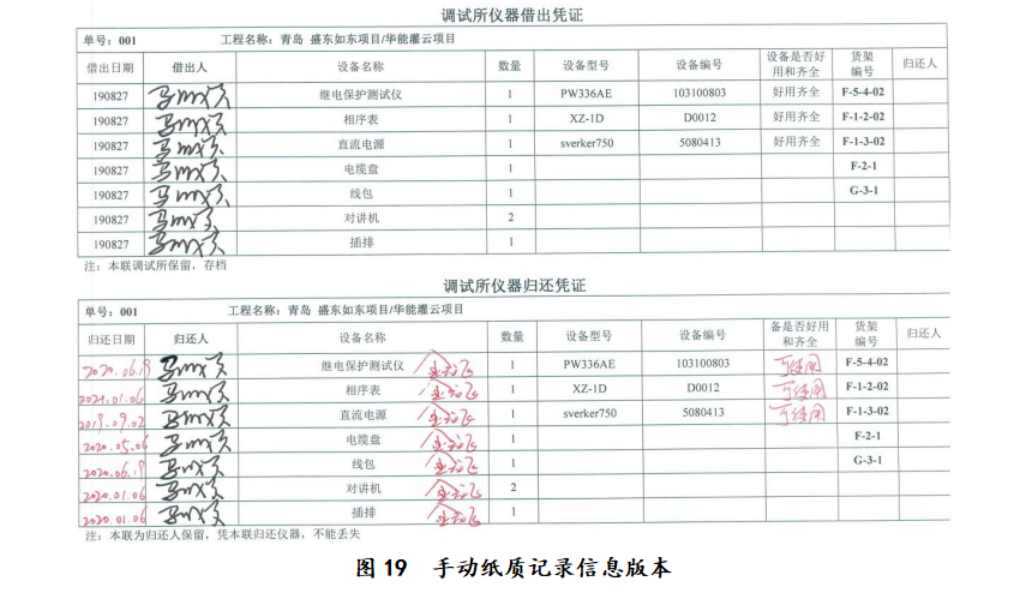
2. Operational Benefits
- Cost Reduction: Eliminated 92% paper documentation
- Global Access: Supported 14 overseas projects across 8 countries
- Compliance: Automated calibration tracking and blockchain notarization
Standardization
- Documentation System
- QR code management handbook
- Standard operating procedures
- Training Program
- On-site workshops for 300+ technicians
- Video tutorials for remote staff
- Maintenance Protocol
- Monthly system audits
- Version control for technical documents
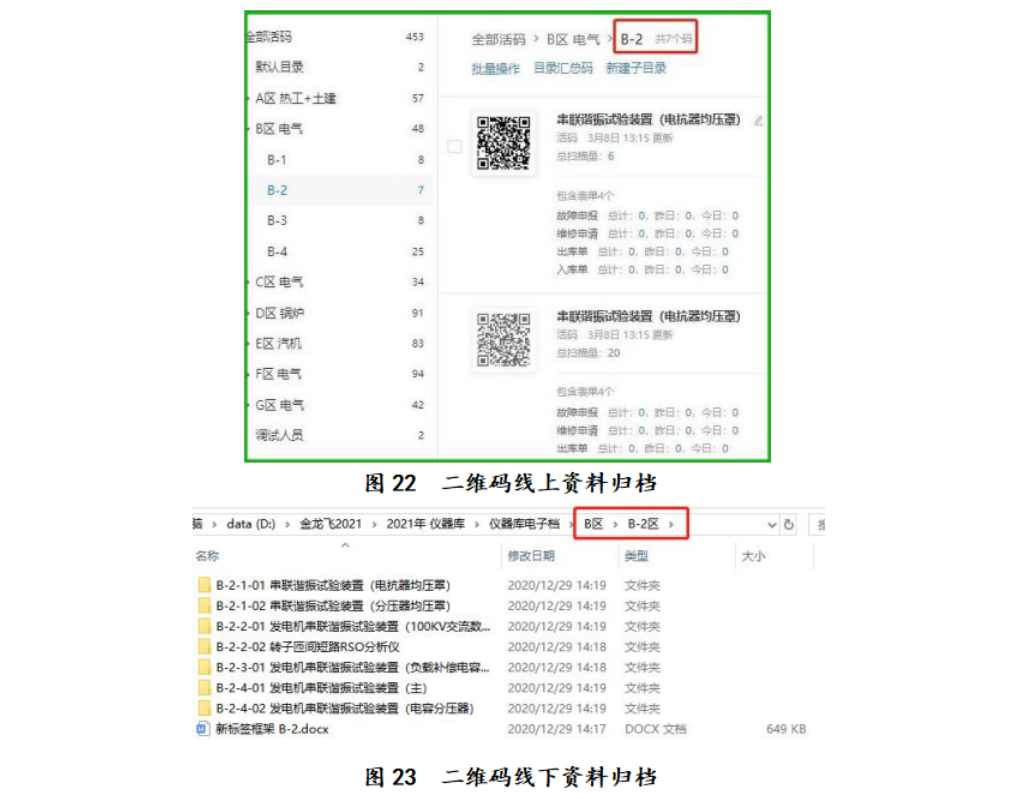
Future Development
Building on this success, we're expanding to:
- AI-powered predictive maintenance
- IoT integration for real-time monitoring
- Facial recognition for contactless access
Our next QC project will focus on Implementing Facial Recognition and QR Code Integration for Unmanned Asset Management.