CaoLiao QR Code Empowers Better Equipment Management Digitalization
Original article: https://cli.im/article/detail/2235
In today's rapidly evolving manufacturing environment, equipment management efficiency directly impacts enterprise productivity and competitiveness. Our company also faces multiple challenges in equipment management processes.
In an era where QR codes are used for shopping and payments, we've implemented a QR code system to manage quality, equipment, safety, projects, and process improvements. This article focuses on how CaoLiao QR Code optimizes Better's equipment management processes, enhancing maintenance efficiency and equipment operation quality.
01 Implementation Planning
First build forms in the backend of CaoLiao QR Code platform, designing functional modules including equipment inspection, maintenance, repair requests, and data dashboards.

Generate QR codes in bulk based on equipment lists, implementing "one code per device". Affix QR codes on equipment for quick access to the system interface.
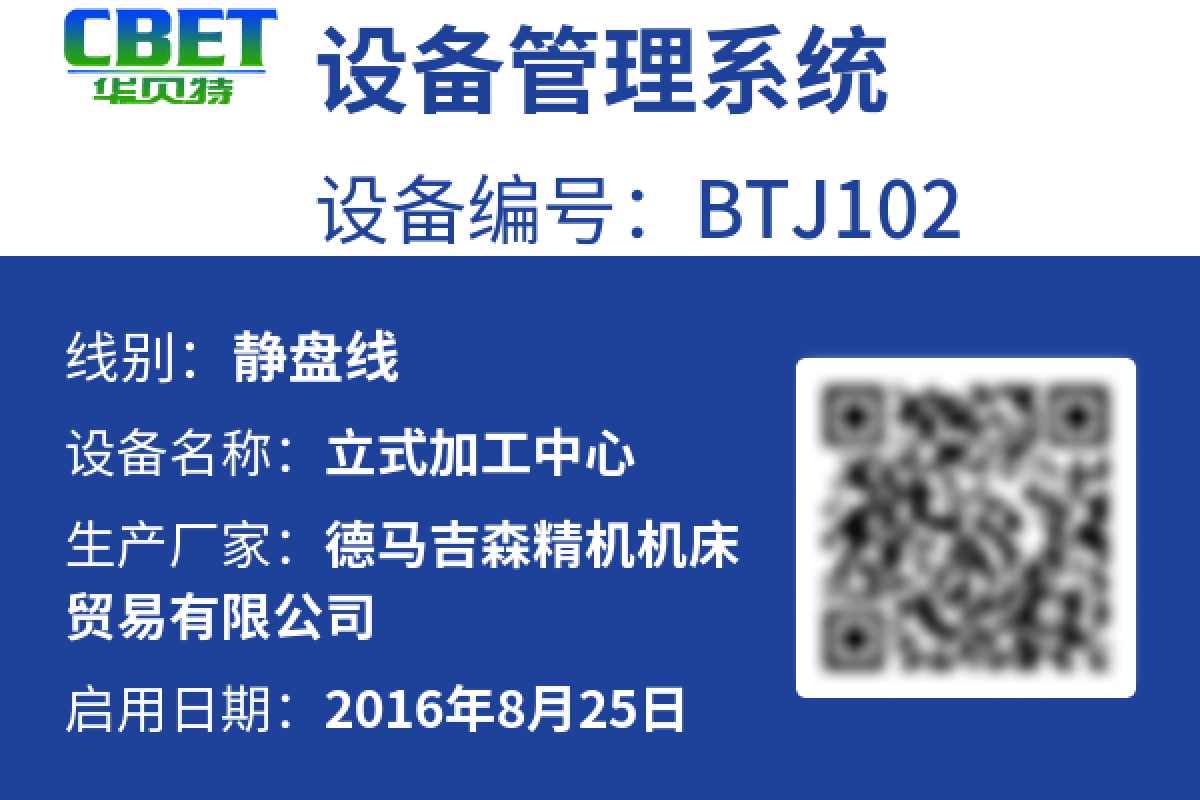
02 Inspection Process Innovation
Drawbacks of traditional paper-based inspections: Checkmark confirmation method cannot guarantee authenticity and completeness of inspections.
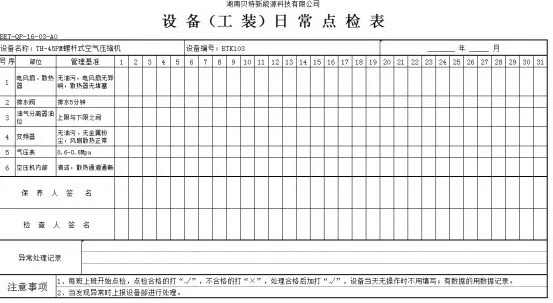
Digital Transformation:
On-site photo documentation: Real-time geo-tagged photos of key parameters during inspections, displaying inspection timestamps to enhance transparency.
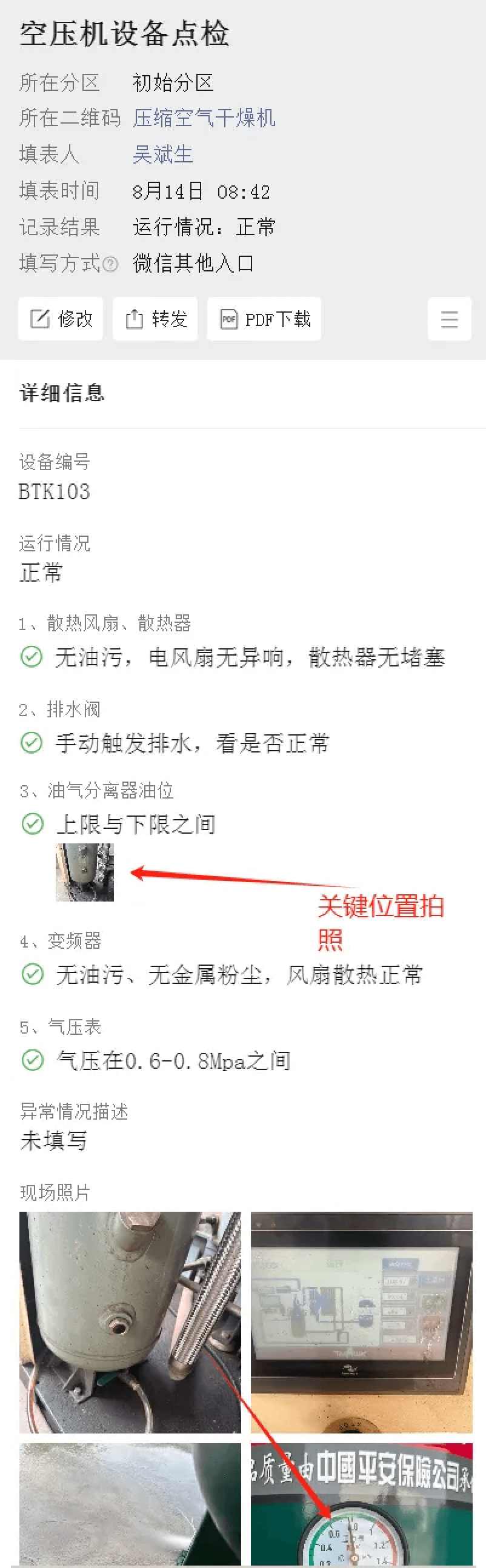
Automated notifications: Push inspection completion alerts to WeChat Mini Program for interactive confirmation, ensuring inspection validity.
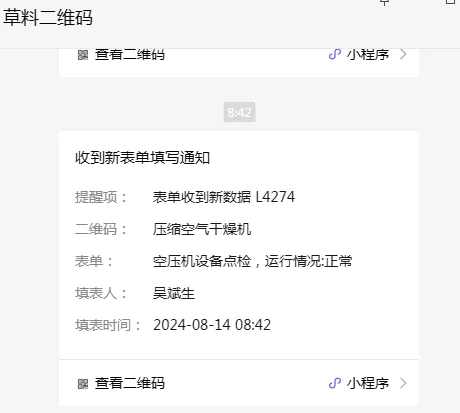
Scheduled reminders: Configure inspection plans with automatic task notifications to reduce omissions and improve compliance.
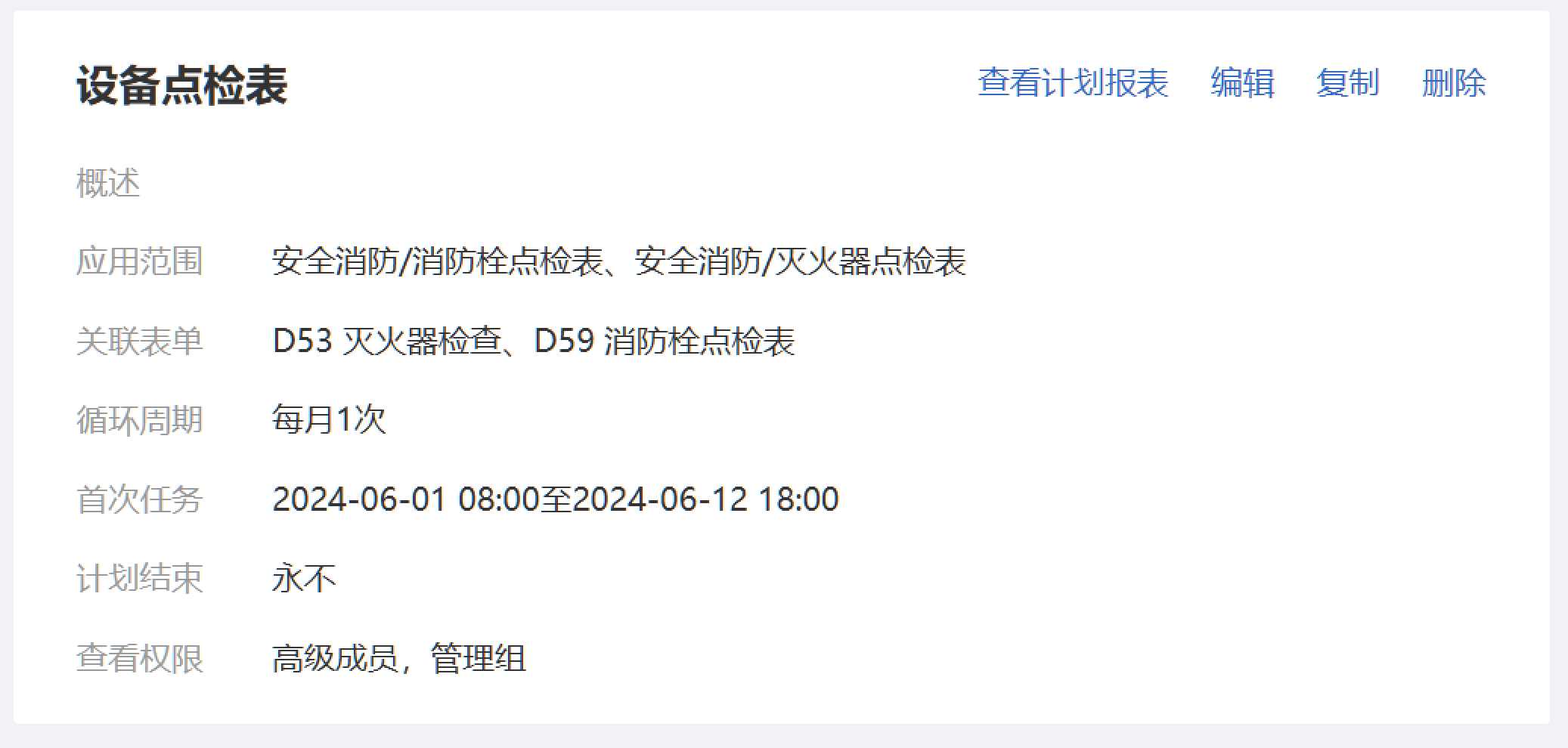
03 Maintenance Management
Challenges of paper-based records: Checkmark-based maintenance confirmation leads to omissions and traceability issues.
CaoLiao QR Code Implementation:
Display maintenance plans and standards: Establish standardized maintenance workflows visible through QR codes based on equipment characteristics.
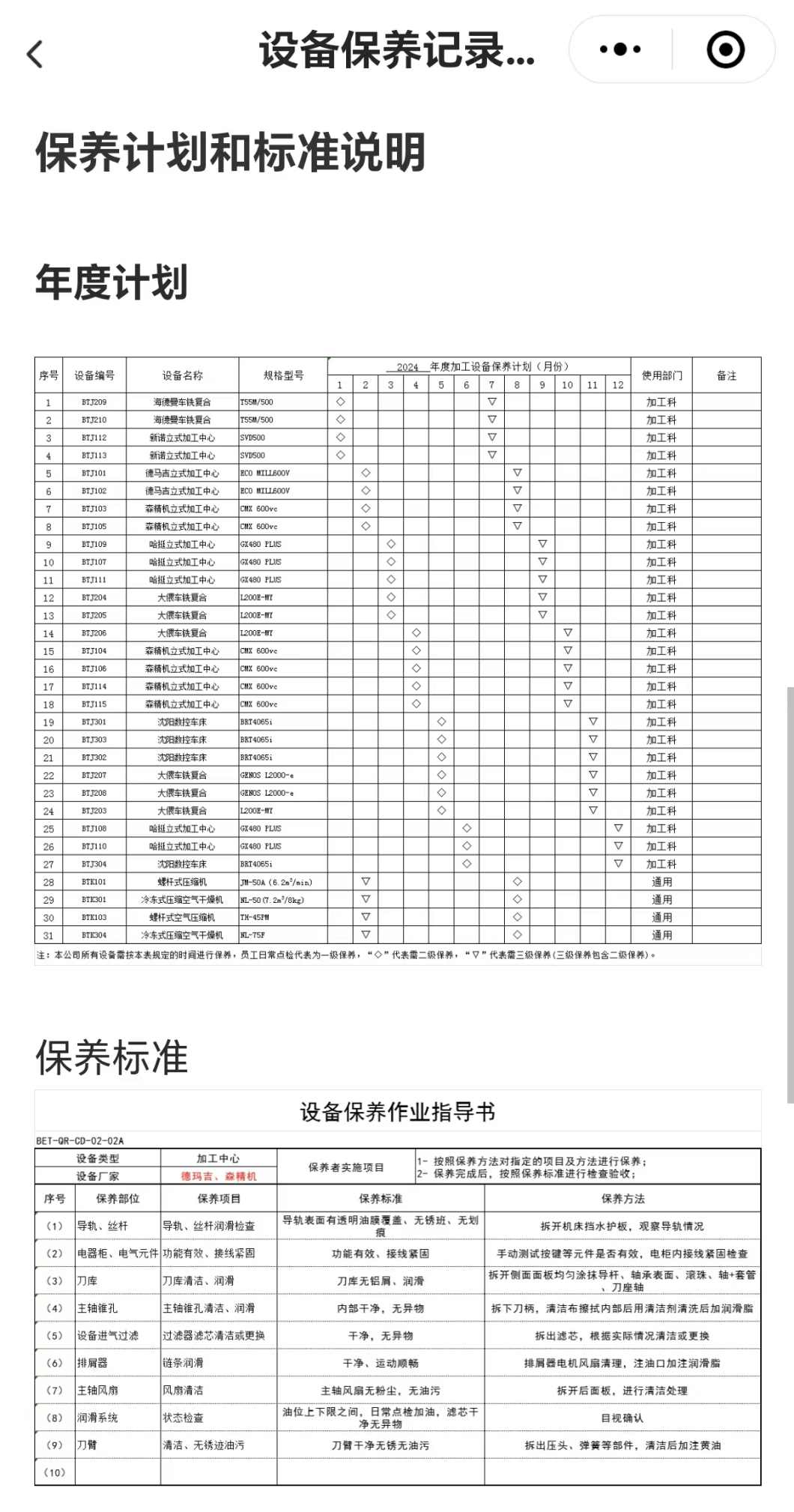
Detailed records: Require pre- and post-maintenance photo documentation via QR code scanning for complete traceability.
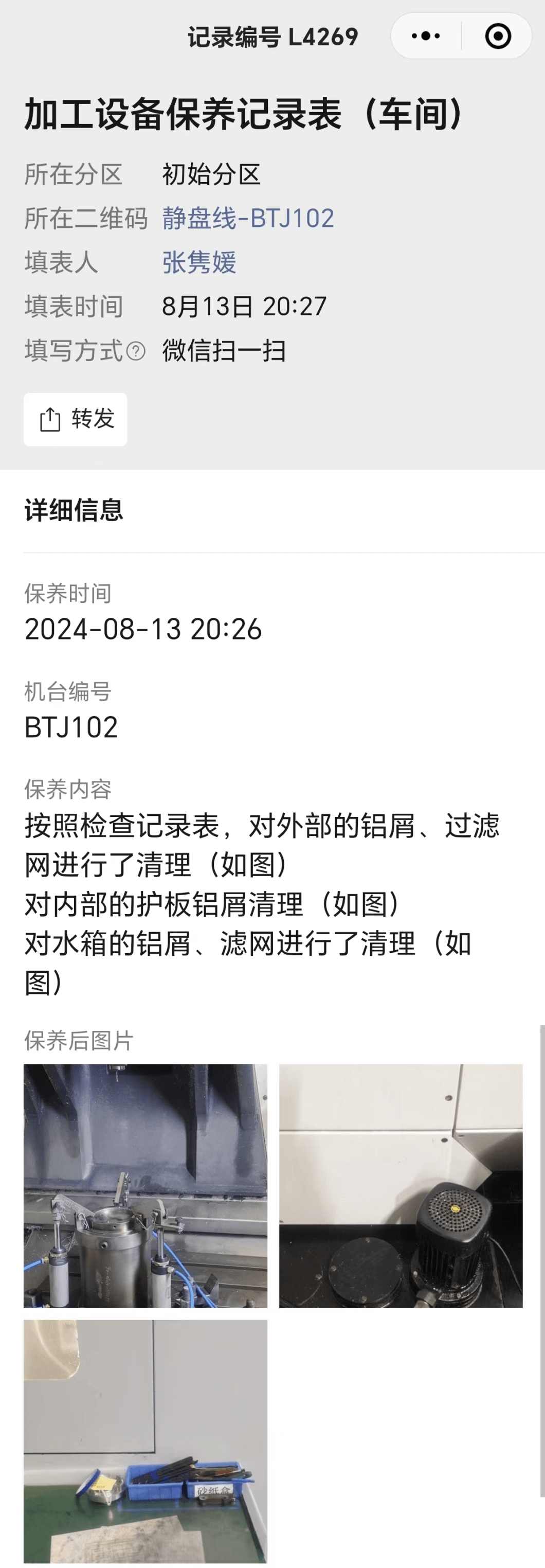
Status notifications: Automatically push maintenance completion details to managers for online evaluation and interaction.
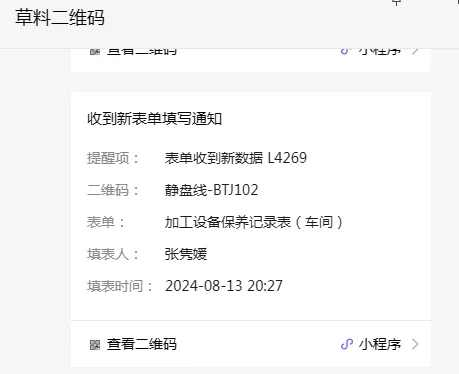
Precision lubrication management: Track oiling operations including quantity, timestamps, and consumption patterns to ensure effective lubrication system operation.
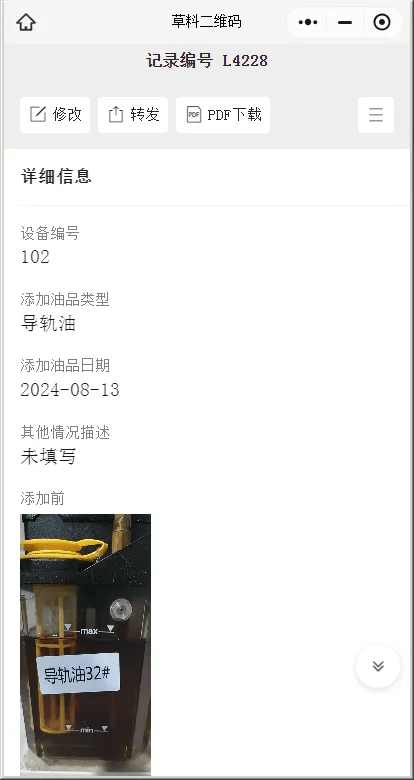
04 Closed-Loop Repair Management
Pain points of traditional repair processes:
- Data timeliness: Slow information transfer in manual processes causes repair delays
- Accuracy: Error-prone manual entries affect repair decisions
- Unverified effectiveness: No mechanism to validate repair quality
- WeChat group limitations: Dispersed historical records hinder long-term management
CaoLiao QR Code Optimization:
QR code-initiated repairs: Each device's QR code enables instant repair requests, automatically marking equipment status as abnormal.
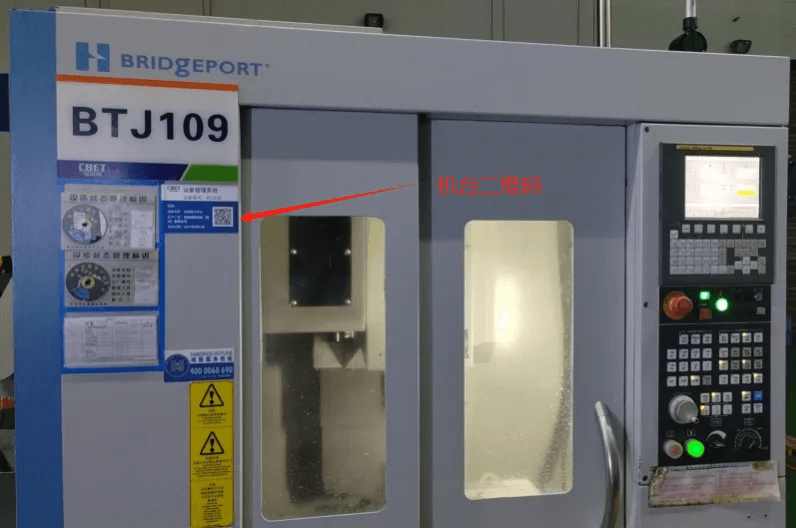
Automatic status update and engineer notification upon repair submission:
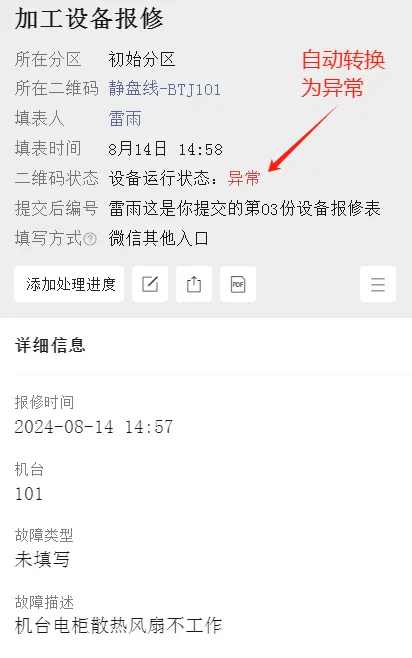
Standardized repair reporting: Maintenance teams use formatted QR code scanning to ensure accurate documentation. Solved issues automatically revert equipment status to normal.
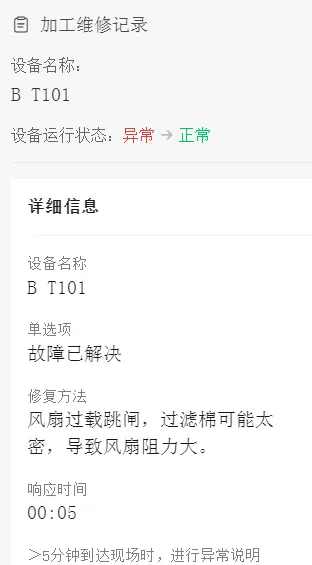
Real-time status updates: Automatic WeChat notifications keep stakeholders informed throughout repair processes.
Full lifecycle management: Digital tracking from inspection through maintenance to repair history.
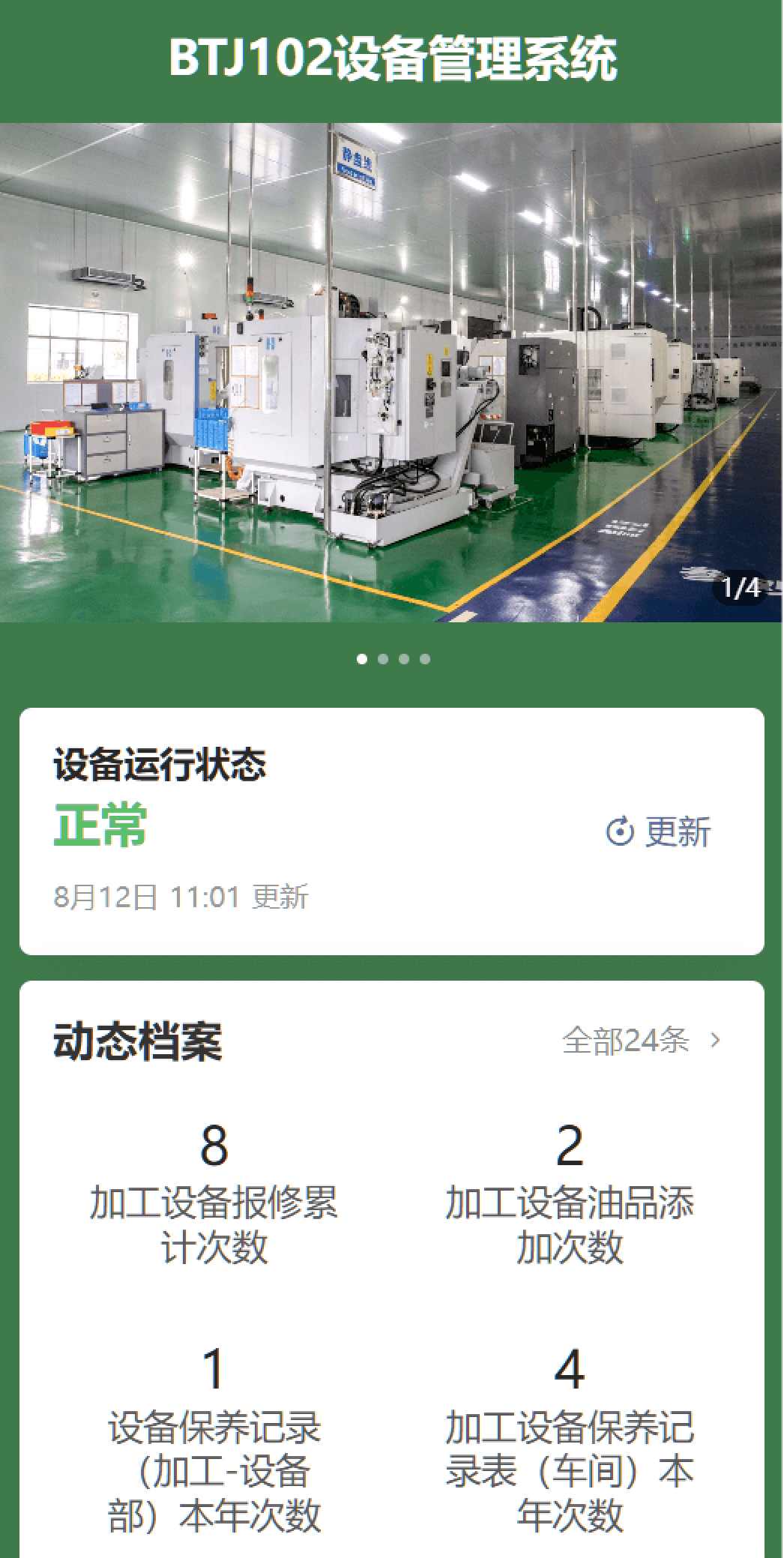
05 Data Dashboard: Decision Support
Real-time equipment monitoring: Status dashboard displays operational conditions and repair progress at a glance.
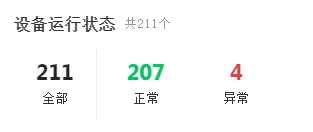
Maintenance alerts: Proactive notifications for upcoming or overdue maintenance tasks.
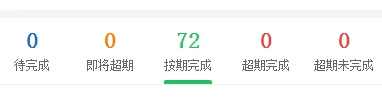
Data analysis: Export backend data for equipment utilization rate reporting and trend analysis.
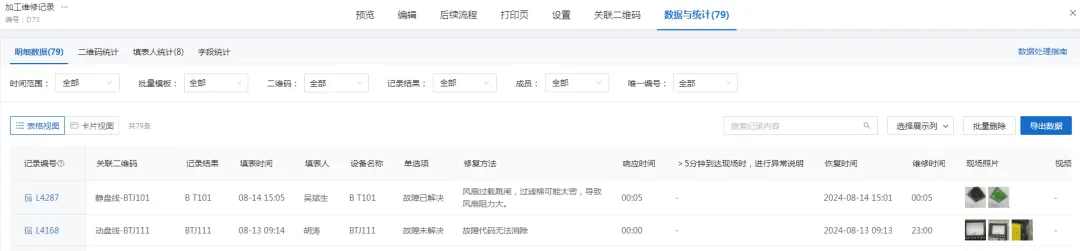
Customized reports: Generate fault analysis reports using predefined templates from exported data.
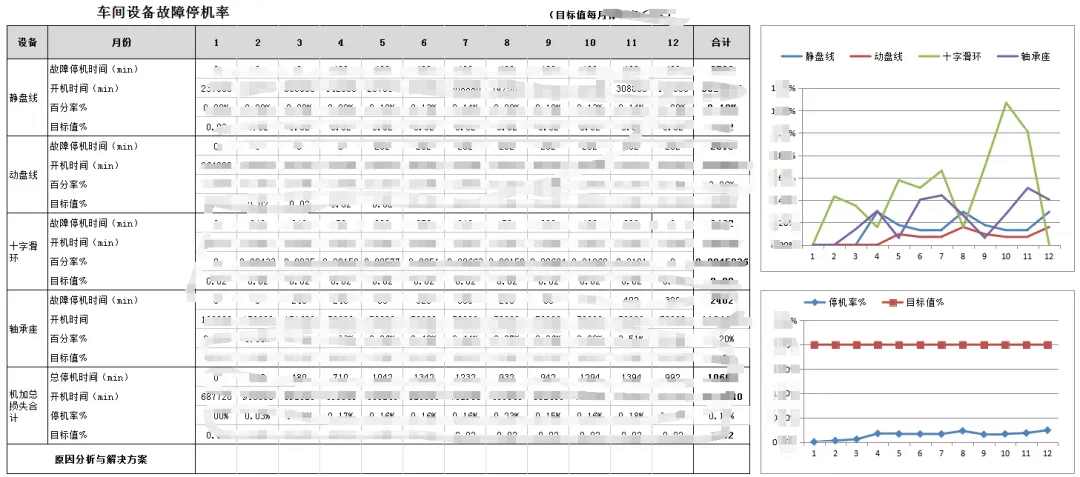
Continuous improvement: Analyze failure intervals and downtime to drive equipment optimization.
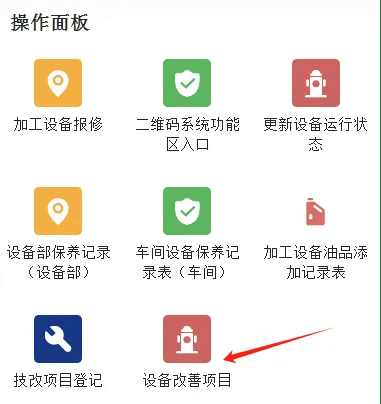
06 Conclusion
CaoLiao QR Code's technical advantages have been deeply integrated into Better's equipment management system. This implementation has streamlined repair processes, enhanced maintenance efficiency and quality, while providing data-driven decision support through comprehensive dashboards. These innovations have propelled Better New Energy Technology Co., Ltd. into a new era of intelligent equipment management.