Pump Room Inspection
One QR code per equipment room, applicable for daily management of domestic water pump rooms and fire pump rooms. Staff members add inspection results based on checkup and maintenance rules. Abnormal conditions trigger immediate alerts to maintenance personnel, shortening fault response time.
Basic Information
- Monthly installations: 3,024
- Monthly visits: 5,838
- Original: https://cli.im/template/detail/65178818
Case Tag Image
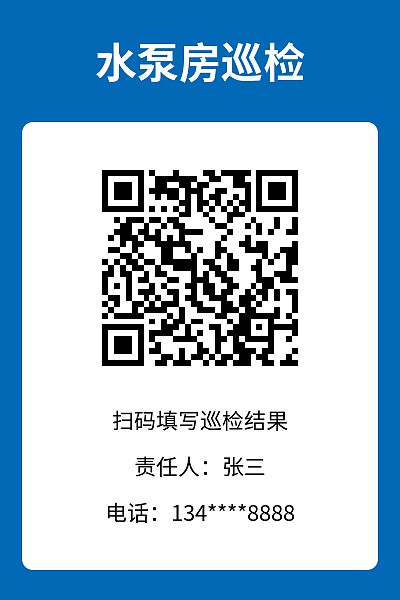
User Guide
1. Problems Addressed
Traditional pump room inspection methods face these challenges:
- Manual record-keeping is error-prone and susceptible to falsification
- Delayed response to abnormal conditions
- Difficulty in aggregating paper-based data
Our solution replaces paper checklists with dynamic QR codes, implementing "one code per device":
- Inspectors scan via WeChat to view device info, perform itemized checks with on-site photos, preventing missed/false inspections
- Automatic alerts to maintenance supervisors for abnormal results
- Data stored in accounts for real-time tracking/export via management backend
This template applies QR codes to pump rooms, with each code printed as a label for inspection initiation.
2. Equipment Profile Access via Scan
One code per device enables instant access to device information:
- View parameters & documentation: Basic specs visible after scanning
- Update operational status: Modify device status based on conditions
- Complete inspection forms: Record checkups item-by-item
- Review historical data: Track past inspections and issues
Note: Additional forms can be added for other recording needs. A single QR code can link multiple forms: checklists, repair logs, equipment startup/shutdown records, etc.
3. WeChat Scanning for Standardized Recording
Inspectors use WeChat to scan and complete standardized forms. Anti-fraud features include:
- On-site photo enforcement: Disable gallery uploads
- Automated photo watermarking: Time/location stamps
- GPS verification: Location tracking
- Blockchain notarization: Tamper-proof data records
Collected data displays on dynamic data panels. View form features
4. Abnormal Condition Handling
System triggers WeChat alerts to maintenance teams for abnormal results:
- Maintenance records: Full documentation of repair processes
- Acceptance confirmation: Validation by quality inspectors
- Process tracking: Complete audit trail for analysis Scenario details
5. Scheduled Inspections with Reminders
Implement maintenance plans (e.g., monthly schedules):
- Next inspection visibility: Display upcoming tasks when scanning
- Mobile progress reports: Completion status tracking for administrators
- Overdue alerts: WeChat notifications before deadlines Feature guide
6. Data Management
6.1 Data Viewing
All submissions stored in account with multiple access methods:
Details
Desktop Workbench
Mobile Workbench (Mini Program)
6.2 Statistics & Export
Access aggregated data through "Data & Statistics" page with filtering by QR codes, submitters, or fields. Details
Export options:
- Excel for further analysis
- PDF for printing/sharing
6.3 Data API Integration
Enable:
- Real-time data pushes to WeCom/DingTalk/Feishu groups
- Custom dashboards via visualization tools Guide
7. FAQs
7.1 Permission Settings
Controllable operations:
- QR code viewing
- Status changes
- Form submissions
- Data visibility
7.2 Multi-device Management
Solutions:
- Advanced members: Paid editions allow assigning management permissions Learn more
- Partition management: Separate devices/types with independent control Guide
7.3 Full Status Monitoring
Automatic status updates (e.g., Normal → Abnormal) visible via:
- QR code pages
- Status dashboards (mobile/desktop)
Details
7.4 Complete Implementation Guide
Client Cases
Wenzhou Central Hospital: Digital IDs for Fire Facilities
Liaoning Guobin Property: QR-based Facility Management
Wuxi Hongdou Property: Vehicle Registration System
Suzhou Rail Transit: Lightweight Smart Management
COFCO Property: Custom Quality Systems
Shanghai Zitai Huisheng Center: Self-built Monitoring